Clientcases
Coenen Transport
The WMS ensures the processes in the automated warehouse run smoothly
A warehouse that is five times as large, yet with the same number of logistical staff as before. The new warehouse of Districenter – part of Coenen Transport – is fully automated. Vanboxtel’s Warehouse Management System (WMS) ensures the various processes in the warehouse all run smoothly.
At home in mechanical operations
“We are entirely dependent on technology in our new warehouse,” says director Theo Coenen. “However, I have no doubt Vanboxtel can pull it off. We have been working together since 2012 for our network and the automation of our office. Because I knew the people at Vanboxtel are also at home in the world of mechanical operations, it made sense for us to use the Vanboxtel WMS in our new warehouse.”
"Although everything is going smoothly, we are constantly working with Vanboxtel to find ways to do things even smarter and better." - Quote client
Relevant solutions with this client case
Vanboxtel-WMS
Support / service
Logistic datapath
Fully operational in under two weeks
Getting a new mechanical warehouse up and running can take months – but not at Districenter. “Following the completion of the warehouse, we were fully operational in under two weeks,” Theo Coenen says. “At Vanboxtel’s recommendation, we work entirely in the cloud. This allowed us to start connecting all our systems to the Vanboxtel WMS even before the construction of our warehouse had begun.” It made it possible to simulate the entire logistical process, including mechanical operations and transport planning. Although the physical warehouse had not been built yet, the pallets and cranes were already in full operation in the digital world.
Smarter and better
The new warehouse has room for 24,000 pallets in cold storage and another 3,500 pallets in refrigerated storage. “We have the option to take our automation to the next level by implementing an automatic picking system. As we continue to grow in the future, our systems will grow right along with us: the WMS is highly scalable. For now, though, our focus is on optimisation. The warehouse has been operational for a year now. Although everything is going smoothly, we are constantly working with Vanboxtel to find ways to do things even smarter and better. We want to make optimal use of our systems.”
A single point of contact and 24/7 support
“In the world of logistics, a malfunction is the last thing you need – especially if your operations are fully automated,” Coenen continues. “We have outsourced all our IT processes to Vanboxtel, with full management via the cloud. If a malfunction does occur, we can count on 24/7 support and a single point of contact.”
Want to know more about the used services?
Want to know more about this case and the services that are offered? Feel free to contact us., we will answer your questions as soon as possible.
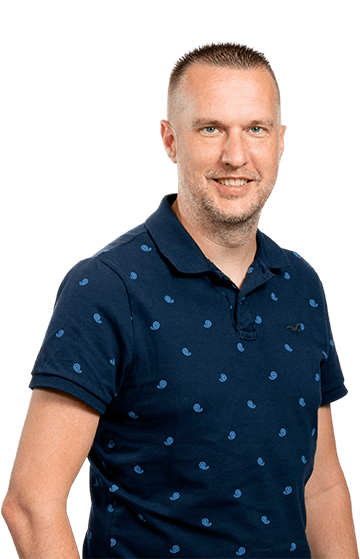